- Joined
- Aug 3, 2014
- Messages
- 38
- Reaction score
- 35
After months of procrastinating, indecision and dealing with higher priority projects I have finally got around to (attempting) building an Impact Mill. I have watched 30 or 40 YouTube videos, researched on line and following a few threads in this forum on the subject, and I think I have got my head around what to build.
I am new to prospecting and I am guessing that there are others in this forum that are just as inexperienced. So I intend to document my approach and add some context to the approach I am taking. I hope that others may be able leverage my experiences or learn from any mistakes along the way.
I decided to use a 274 mm X 10 mm hardened steel pipe as my starting point. I am not lining the pipe with hardened plate at this stage, I want to see how the mill wears with use. The following illustration is what I am hoping it will look like when completed.
So my starting materials consist of a couple of 25mm bearings (including housings), a 2020 X 300 X 10 mm steel plate, a couple of meters of 10x40 Flat Bar and 50x50x6 Angle; and the pipe.
After a couple of hours work I managed to get the end plates cut and welded to the pipe. The whole thing was cut in two, ready for the next stage; building the support frame. Below are a few photo's of the process. I will update this thread over the next couple of weeks as the project progresses.
Rick
Cutting the end plates (with jig).
The pipe with end plates welded.
The two halves of the Mill....
I am new to prospecting and I am guessing that there are others in this forum that are just as inexperienced. So I intend to document my approach and add some context to the approach I am taking. I hope that others may be able leverage my experiences or learn from any mistakes along the way.
I decided to use a 274 mm X 10 mm hardened steel pipe as my starting point. I am not lining the pipe with hardened plate at this stage, I want to see how the mill wears with use. The following illustration is what I am hoping it will look like when completed.
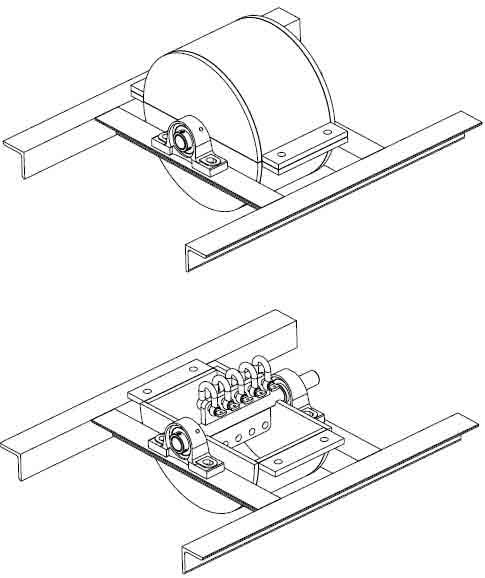
So my starting materials consist of a couple of 25mm bearings (including housings), a 2020 X 300 X 10 mm steel plate, a couple of meters of 10x40 Flat Bar and 50x50x6 Angle; and the pipe.
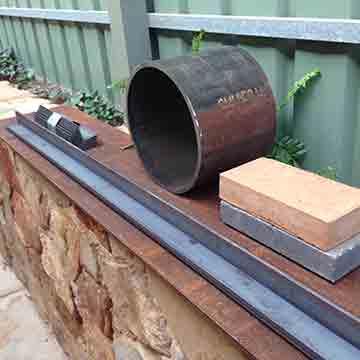
After a couple of hours work I managed to get the end plates cut and welded to the pipe. The whole thing was cut in two, ready for the next stage; building the support frame. Below are a few photo's of the process. I will update this thread over the next couple of weeks as the project progresses.
Rick
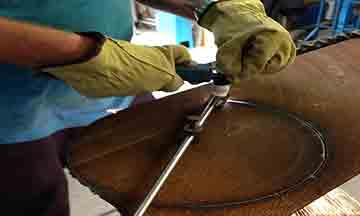
Cutting the end plates (with jig).
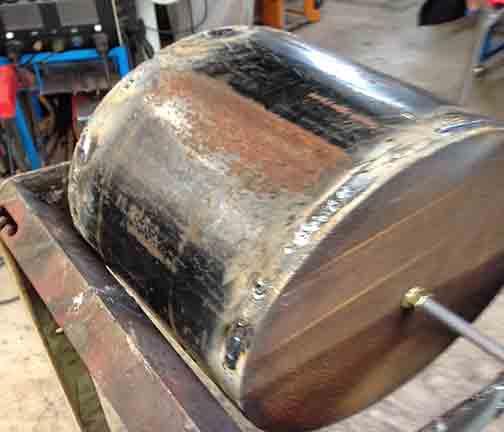
The pipe with end plates welded.
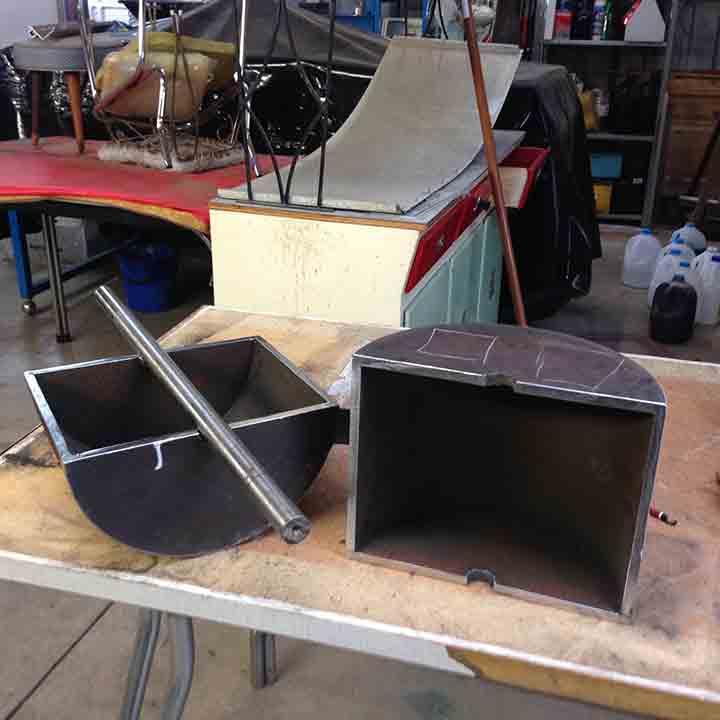
The two halves of the Mill....