Syndyne
Shaun Galman
Hi all,
Some absolutely awesome ideas and builds on here! I'll throw in my own little project that came to fruition almost a year ago to the day.
After using the Angus Mackirk sluices for a couple of years now with a great ease of use (coming from the old Fred Sims designed aluminum banjo sluice after purchasing what I think were some of his first prototypes down at Adelong when we met him there in the very early 80's) I looked into the AM Boss Sluice for a slightly faster feed rate. Once it arrived I had the idea that it may make a pretty decent highbanker. So I did a few weeks of research and drew up several plan variations and narrowed it down to something portable and very light that can be broken down enough to fit in our large tool box that we carry all the gold gear in safely.
With this in mind I whipped up a frame that fit the sluice with no attachment. This allows us to just take the sluice out, empty it into a pan for clean-up then throw it back in to keep working if needed. I had a couple of metres of 1/2 inch (12mm) dia. x 1/8 (2.5mm) thick box channel so I welded it up and added the legs/leg brackets. Frame done.
I drew up some rough plans for the boiler box, headed to Albury meet up with my friends, got some 1/8" aluminum sheet, 1/2" expanded mesh and the pipes from Bunnings -boy they make life easy there as far as these projects go! Nothing like that out this way.
We then sat down, exchanged thoughts and laid it all out. After several coffee's, some TIG work, drilling and filing over four hours or so we were all done. (The boys I grew up with here are both first class ally and stainless welders now living in Albury). That was a nice bonus that I really appreciate now as the TIG welding alone would've cost me a packet.
We made the boiler box simply clip on the back of the sluice with hooks and we attached an aluminum shelf guide with a stainless hinge as a front clipping section which turned out to allow plenty of angle adjustment of the boiler box. We supported that with a piece of right angle to easily spread the weight of anything in the boiler box evenly across the sluice frame. Then I just hold the water pipes in place with removable cable ties. We use a Tanaka TCP-25B 110L/min 2stroke pump and 60feet of marine flex hose. I normally only run the pump about half throttle.
The last shot was taken of my father and I doing initial testing on the Buckland River. Worked like a beauty. We never saw any gold get past the fourth riffle with a decently fast feed rate. Over the weeks we moved around and worked different towns with varying conditions like heavy clay, a lot of black sands etc. and had no dramas at all.
Any and all thoughts/comments are highly appreciated.
Cheers,
Shauno.
*Edited for spelling correction
Some absolutely awesome ideas and builds on here! I'll throw in my own little project that came to fruition almost a year ago to the day.
After using the Angus Mackirk sluices for a couple of years now with a great ease of use (coming from the old Fred Sims designed aluminum banjo sluice after purchasing what I think were some of his first prototypes down at Adelong when we met him there in the very early 80's) I looked into the AM Boss Sluice for a slightly faster feed rate. Once it arrived I had the idea that it may make a pretty decent highbanker. So I did a few weeks of research and drew up several plan variations and narrowed it down to something portable and very light that can be broken down enough to fit in our large tool box that we carry all the gold gear in safely.
With this in mind I whipped up a frame that fit the sluice with no attachment. This allows us to just take the sluice out, empty it into a pan for clean-up then throw it back in to keep working if needed. I had a couple of metres of 1/2 inch (12mm) dia. x 1/8 (2.5mm) thick box channel so I welded it up and added the legs/leg brackets. Frame done.
I drew up some rough plans for the boiler box, headed to Albury meet up with my friends, got some 1/8" aluminum sheet, 1/2" expanded mesh and the pipes from Bunnings -boy they make life easy there as far as these projects go! Nothing like that out this way.
We then sat down, exchanged thoughts and laid it all out. After several coffee's, some TIG work, drilling and filing over four hours or so we were all done. (The boys I grew up with here are both first class ally and stainless welders now living in Albury). That was a nice bonus that I really appreciate now as the TIG welding alone would've cost me a packet.
We made the boiler box simply clip on the back of the sluice with hooks and we attached an aluminum shelf guide with a stainless hinge as a front clipping section which turned out to allow plenty of angle adjustment of the boiler box. We supported that with a piece of right angle to easily spread the weight of anything in the boiler box evenly across the sluice frame. Then I just hold the water pipes in place with removable cable ties. We use a Tanaka TCP-25B 110L/min 2stroke pump and 60feet of marine flex hose. I normally only run the pump about half throttle.
The last shot was taken of my father and I doing initial testing on the Buckland River. Worked like a beauty. We never saw any gold get past the fourth riffle with a decently fast feed rate. Over the weeks we moved around and worked different towns with varying conditions like heavy clay, a lot of black sands etc. and had no dramas at all.
Any and all thoughts/comments are highly appreciated.
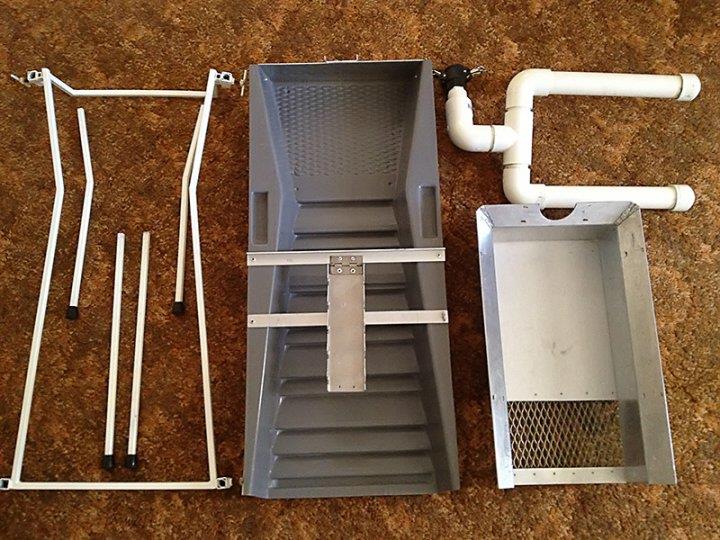
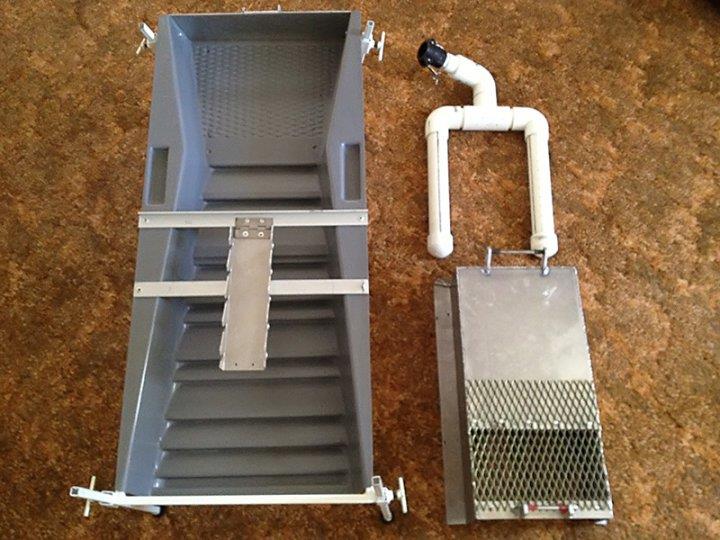
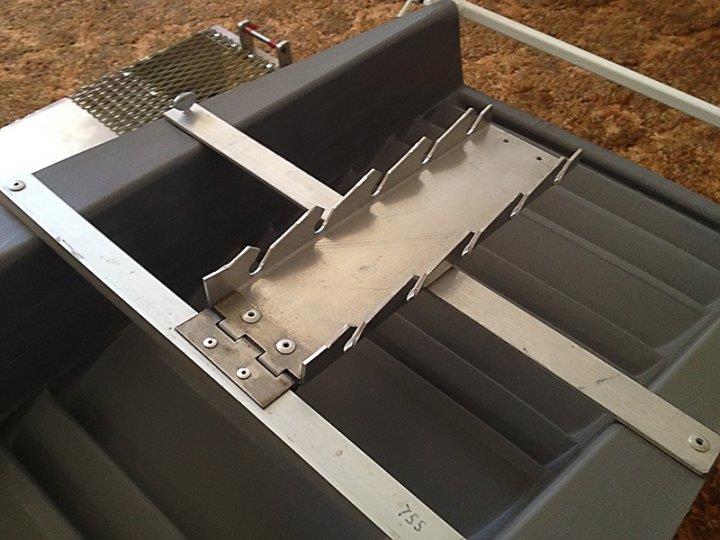
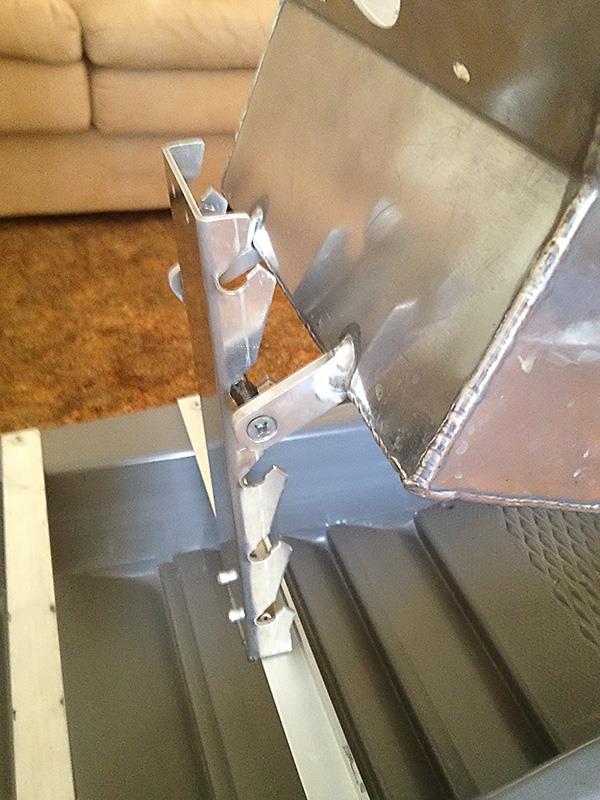
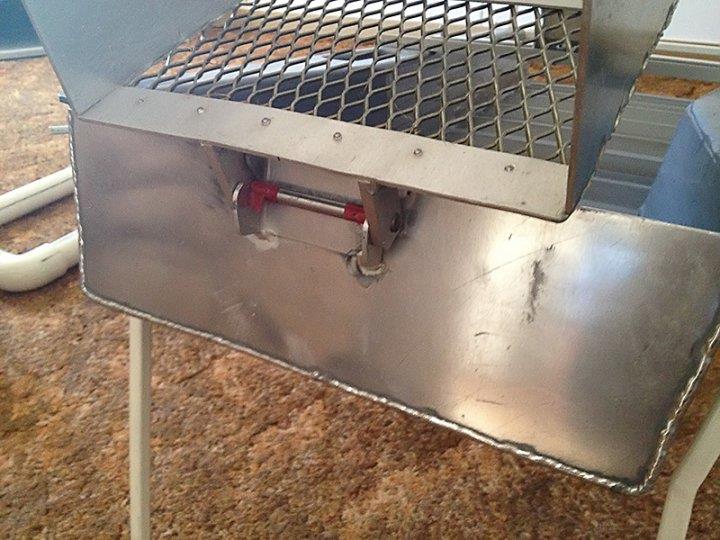
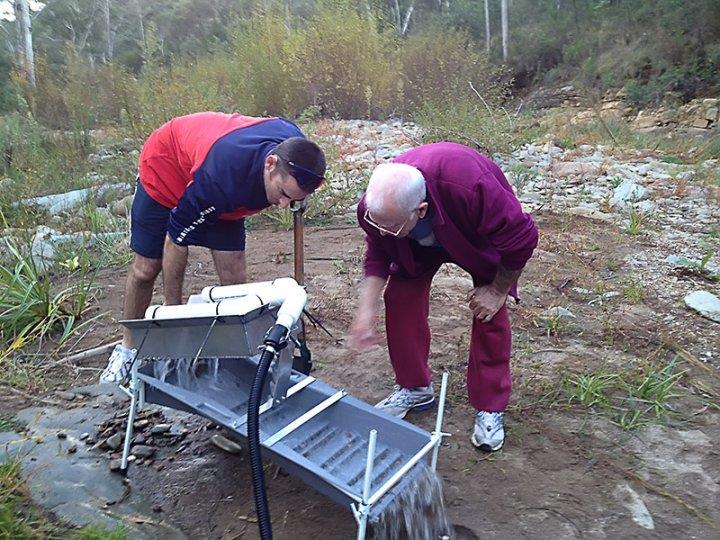
Cheers,
Shauno.
*Edited for spelling correction